High-Speed Steel T-Slot End Mills Use these end mills for general purpose work in most material, such as aluminum, brass, bronze, iron, and steel. They're often used to create slots in machine tool tables, indexing tables, and other workholding surfaces. You can cut a slot with a table saw - place the work piece accordingly - raise the blade until you have the appropriate length slot - then lower the blade. You do end up with non square ends though - which may be a problem. The slot is only 1/2' long. This could pose a problem with a 7-1/4' blade. Just clamp the steel down in a good solid vice, and drill firmly, with authority, through the steel with hardened steel bits. Have a helper constantly apply coolant or oil while you're drilling, this is why the can of WD-40 is in frame.) Bolt the steel angle onto the strap iron using appropriately sized bolts. Seen from the side/back.
All the aspects of high speed machining can be a real challenge to wrap your head around. Filtering through what's real and what's just a buzzword can be a chore in and of itself.
So is peel milling a technique worth learning?
Best poker quotes and sayings. Definitely.
Peel milling is an approach that uses high feed rates, low radial depth of cut and high axial depth of cut. It relies heavily on the principle of chip thinning, using a tool path that maximizes tool wear along the entire flute length.
Trochoidal milling is a particular type of motion – a circular high speed maneuver that is excellent for carving out deep slots and other narrow features. Incorrectly used, though, it can waste a lot of time.
Ok, that was pretty packed with information. Let's break that up and use a few diagrams to explain what's going on, how to do it properly, and how to know when your application justifies it.
Peel Milling Principles
The basic idea here is to use a small stepover, usually around 10% of the tool's diameter, but max out the Z depth.
Of course, when using this method in the real world, you're best off consulting the cutting tool manufacturer for recommended cutting parameters, but these numbers are usually pretty realistic.
For example, if you have a 0.500″ endmill, you'll cut at a depth of 1.0″ but with a stepover of 0.050″. Compare that to a standard approach of cutting with a depth of 0.250″ and a stepover of 70%, or 0.350″.
Now if we look at the area of cutting engagement, we can work out what kind of stock removal we can get.
For the standard milling approach, we're cutting an area that's 0.250″ x 0.350″, or an area of 0.0875 square inches.
For the peel milling approach, we're cutting an area that's 0.050″ x 1.000″, or 0.050 square inches.
At this point, it's not too impressive, is it? Peel milling doesn't have nearly the same engagement as the traditional approach.
But there's a secret sauce.
Peel milling can take advantage of something called chip thinning.
If you take a look at the size of chip that you get with such a low radial engagement, you'll realize that it's actually super thin. What this means is that you can crank up the feed rate to get a normal chip thickness.
According to those sketches, you can cut the material with a 70% higher feed rate and have the same chip thickness as the 'traditional machining' model.
Now let's convert those previous examples from 2D area to 3D volume.
To do this, we'll need to add some material data to come up with realistic feed rates. Let's say that we're cutting 4140 HTSR. We'll use a cutting speed of 400 SFM for standard machining. Let's see what that stock removal looks like.
For conventional machining, the RPM works out to 3200 RPM. We'll use a feed rate of 0.003″ per tooth, using a standard 4 flute endmill. This means that we'll be feeding the cutter at 38.4 inches per minute.
Taking that same cut of 0.250 deep x 0.350 stepover, our 2D cut is 0.0875 square inches. To convert that to cubic inches per minute, we'll multiply that by our feedrate.
0.1875 square inches x 38.4 inches per minute = 3.36 cubic inches per minute.
Now let's compare that to peel milling.
To maintain the same 0.003″ chip thickness at 0.050″ stepover, the feed can be increased to 0.0051″ per tooth. Another perk of peel milling is that the RPM can also be bumped up.
So let's increase that RPM to 500 SFPM, using a 0.0051″ chip per tooth. This works out to 4000 RPM, and a feed rate of 81.6 IPM. As mentioned previously, the 0.050″ stepover and 1.000″ depth of cut works out to an area of 0.050 square inches.
0.050 square inches x 81.6 inches per minute = 4.08 cubic inches per minute.
That's about 15% faster material removal than the traditional approach. But the advantages of peel milling don't end there.
Maximizing Tool Wear
One of the real disadvantages of the traditional roughing approach is that wear is very concentrated to the bottom of the end mill.
Using that same previous example, what would our endmill look like after an hour of work?
The bottom 0.250″ would be worn out, and the top 0.750″ would be totally fresh. Not really maximizing the use of the tool, is it? Now aside from the cost of the endmill itself, add the down time of the machine operator swapping the tool for a fresh endmill. Overall, it's just not an efficient method.
Now compare that to the tool that's used for peel milling. What would that tool look like after an hour? Instead of all the wear focused on 25% of the tool, the wear would be evenly distributed across the entire flute length.
Also, because of the small radial engagement, the individual flutes are actually in the cut for less time. Let me illustrate.
To put it simply, the actual working time of the cutter's flutes is about 1/3 of the time for peel milling compared to traditional milling.
Does this mean that your cutters last 3x as long? Not always, in my experience. But I do tend to improve tool life noticeably, especially in hard to machine materials like titanium, inconel and cobalt chrome.
Trochoidal Peel Milling Toolpath
In the previous examples, peel milling was used to clear out easily accessed material. But what if you need to cut a deep slot? Can you still use the principles of peel milling?
Definitely. This is where trochoidal peel milling comes in.
To begin, let's look at what a trochoid is.
The Trochoid
Here's the basic concept of a trochoid:
Imagine swinging a weight over your head at the end of a rope while you walk forward. That basic motion of a point rotating around a center and moving forward is a trochoid.
Here's an illustration of the motion:
What you essentially get is a carving motion. For toolpaths, the forward advancement is low, but the 'spinning' motion is done at high speeds. This is what keeps the cutting pressure light.
Here's an example of what one of these toolpaths looks like in a CAM system:
As you can see there, rapidly feeding the tool forward with sweeping motions can maintain a consistent radial engagement.
Chip Clearance
Trochoidal milling is a really effective approach for tight areas where chip clearance would be an issue.
With traditional milling, it can be difficult to evacuate thick, heavy chips from deep features like pockets. This means that these chips will be cut again as the tool feeds around within the feature.
This additional, uncontrolled cutting of metal chips not only adds substantial wear and tear on the cutting tool, but it also adds instability to the operation. A buildup of chips can unexpectedly snap the cutter in half.
Trochoidal milling is an excellent way of clearing chips out of deep features. Instead of the thick, heavy chips of conventional milling, chips from peel milling are long, slender and light. That means that coolant pressure or an air blast can easily clear them away from a workpiece.
One thing worth noting, though, is that peel milling chips are made really fast. This means that your coolant or air pressure needs to be very reliable. If there are any hiccups in delivery, things will go south fast.
What's Required for Peel and Trochoidal Milling?
I know a lot of guys that have tried this with standard tools that are intended for traditional machining. Then when something blows up, it's (in their opinion) because peel milling is a gimmick and doesn't work.
I can assure you that it works very well, but you need to make sure that you're using the right tools and equipment.
Tool Holders
Peel milling puts a lot more pressure on the tool, and has the potential of being a nightmare for vibration. Your tool holder needs to be really solid to be able to handle this high performance milling.
What does this mean?
Don't use weldon shank or ER collet end mill holders.
Seriously, you will pretty well never have great results with these. They just don't hold the tool firmly enough and dampen vibration. Even if you use a 48″ cheater bar.
Aside from the really high speeds and feeds that you'll achieve with peel milling, tools have a tendency of pulling out. This is because the teeth are hitting the workpiece so aggressively that the helix of the flutes will push the cutter down and out of the tool holder. Weldon shank holders and ER collets do very little to resist this.
My favorite option for this is a good quality hydraulic tool holder, although I've also had very good success with shrink fit systems.
What I like about the hydraulic tool holders is their versatility and vibration dampening qualities. They don't have the tendency to ring at certain frequencies like other systems do. And, to fit up an endmill of a different diameter, you only need to change the sleeve.
Shrink fit systems are also excellent. The clamping force of the steel body once cooled down is insane, so tools clamped in this way are really rigid. The disadvantage to this is that you need a system for heating the holders up to change the endmills. This can be a pretty hefty startup cost, so it's a bit of a commitment for shops to gain this capability.
One technology worth looking in to is Safe-Lock from Haimer. This is a really amazing way of stabilizing carbide endmills and making it essentially impossible for cutters to pull out from the tool holder. You'll notice that you can push the tool much harder with a system like this.
Even though Haimer is the one that holds the patent to that technology, they make it available to other tool manufacturers through license, so you will see this offered by other brands.
Specialized Cutters
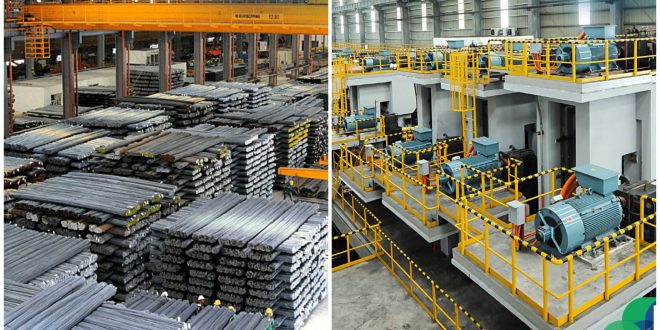
Here's another interesting aspect of peel milling: The chips are always slender and thin.
We can use this to our advantage when it comes to cutter selection. This isn't so much an absolute requirement, but it will help you take advantage of the high performance capabilities of peel milling.
The traditional approach of thick, heavy cuts meant that the tools needed a large amount of space between flutes for chip clearance. These chips needed somewhere to go, so large gaps needed to be designed into these cutting tools to accommodate them.
With peel milling, you don't need that massive chip clearance.
What this means is that two things are possible: Best slot receivers in nfl history.
- The flutes don't need to be as deep on a cutter, so the core diameter can be substantially thicker. This means that you can use a much stronger tool and push it significantly harder.
- You can use more flutes. Instead of a standard 4-flute endmill, many tools designed for peel milling have 6 or 8 flutes. This alone can potentially double the possible feed rates.
Now considering the example we had mentioned before comparing traditional vs peel milling, we can see that with specialized tools, we can get significantly more efficiency out of peel milling.
This is why many shops have been able to double their material removal by investing in specialized equipment.
High Speed Mills
If you have a tired, old machine from the '80's, you might not be too impressed with it's interpretation of peel milling.
Especially for things like trochoidal milling, you need a fast machine. And not just maximum feed rates, either.
A machine needs to be able to handle hard acceleration and deceleration, or else you'll never get up to speed. You might notice on your machine that when you're doing tight corners, the feed rate that's displayed on the controlled is often constantly changing, slowing down on sharp turns.
How To Mill Slots In Steel Drums
Your mill needs to be able to make small, fast movements accurately. For most machines, you can punch in a line of code that will change the modes – from high speed mode to exact stop mode and everything in between. In high speed mode, it needs to be able to honor the programmed toolpath without significantly overshooting.
Otherwise, you'll have a lot of broken tools when your machine ends up overshooting and pushing your tool 0.080″ into the material instead of the intended 0.050″.
Aside from having fast, responsive servos to handle sharp changes in direction quickly, your machine needs to be a fast thinker.
For high speed machining, you might end up with programs with millions of lines of code. If your machine controller can't read the code fast enough, then all your potential efficiency from peel milling will be lost while your machine tries to figure out its next move.

Machines that are well equipped for high speed machining will advertise a high 'block look-ahead', often something to the tune of 10,000 blocks.
What this means is that the controller will read 10,000 blocks ahead of the current block to be able to 'plan out' the most efficient way of hitting this toolpath within the allowable tolerance. If your machine doesn't have this ability, then you might find that your feed rate never actually hits what you programmed it to be.
Cam System
This is fairly straightforward. In order to benefit from peel milling, you need to have software that is capable of it.
The good news is that peel milling has been around for a while, so the large majority of decent CAM packages will have something to offer.
They're not all created equal, though. Some allow you to have a tighter control than others. If you're looking at a CAM package for your shop, take your time and see how good both the CAM toolpaths and the postprocessed results are.
The reason that I say to pay attention to the postprocessor is that with peel milling, you will have a lot of small movements. You want this to be calculated accurately as arc commands (or splines if your machine has a Siemens controller) without rounding issues. If you have to resort to using G1 line motions because you keep getting errors on your machine controller saying that there's a problem with your G2 and G3 values, you won't be a happy camper.
Really, this is becoming less and less as a factor as peel milling becomes more mainstream, but even still, it's a factor to pay attention to.
When is Peel Milling Practical?
There's a reason that this isn't the only operation you can select in your CAM software: while it is a great solution, it can't be applied to everything.
Peel milling works best when you can really sink your tool deep in the material. In other words, if you're doing shallow pocketing, you'll be better off with another strategy.
How To Mill Slots In Steel Cut
Slotting
Trochoidal milling is very often the best solution for slotting, but again it really does depend on the feature geometry. For example, the slot might be so deep that the only reasonable way of cutting it is either with a slitting saw or an EDM. If the slot is 0.050″ wide x 1.000″ deep, no endmill will help you.
I find the sweet spot for trochoidal slotting to be where you can maximize the depth of an endmill that's between 50-75% of the slot width. In other words, a half inch endmill with a trochoidal toolpath will be an excellent choice for a slot that's 0.75″ wide and 1.000″ deep.
Pocketing
This is an excellent choice for deep pockets. The thin, light chips are easily blasted out of the pocket with and air blast or high pressure coolant, and the material removal rate is very high if you can use the full flute length.
Hard or Exotic Materials
When I'm roughing titanium, I use one of two methods: plunge milling or peel milling.
The material removal rates of plunge milling in titanium are second to none, but the leftover scallops can be a pain to clear out. They often require an excess of semi-finishing operations before you can run your finishing tool to complete the feature.
Peel milling, on the other hand, can often rough and finish in a single operation. Especially for deep and narrow features, it's hard to beat.
Peel milling really shines when it comes to hard and abrasive materials. Since it distributes wear along the entire flute length, it can be a great solution in applications where notch wear or chipping is common. Here are some materials where you should seriously consider using peel milling as a practical way of roughing:
- Titanium
- Inconel
- Cobalt-Chrome
- Hardened tool steels (above 50 Rc)
- In general, any material that is work-hardening, abrasive, or hardened.

Here's another interesting aspect of peel milling: The chips are always slender and thin.
We can use this to our advantage when it comes to cutter selection. This isn't so much an absolute requirement, but it will help you take advantage of the high performance capabilities of peel milling.
The traditional approach of thick, heavy cuts meant that the tools needed a large amount of space between flutes for chip clearance. These chips needed somewhere to go, so large gaps needed to be designed into these cutting tools to accommodate them.
With peel milling, you don't need that massive chip clearance.
What this means is that two things are possible: Best slot receivers in nfl history.
- The flutes don't need to be as deep on a cutter, so the core diameter can be substantially thicker. This means that you can use a much stronger tool and push it significantly harder.
- You can use more flutes. Instead of a standard 4-flute endmill, many tools designed for peel milling have 6 or 8 flutes. This alone can potentially double the possible feed rates.
Now considering the example we had mentioned before comparing traditional vs peel milling, we can see that with specialized tools, we can get significantly more efficiency out of peel milling.
This is why many shops have been able to double their material removal by investing in specialized equipment.
High Speed Mills
If you have a tired, old machine from the '80's, you might not be too impressed with it's interpretation of peel milling.
Especially for things like trochoidal milling, you need a fast machine. And not just maximum feed rates, either.
A machine needs to be able to handle hard acceleration and deceleration, or else you'll never get up to speed. You might notice on your machine that when you're doing tight corners, the feed rate that's displayed on the controlled is often constantly changing, slowing down on sharp turns.
How To Mill Slots In Steel Drums
Your mill needs to be able to make small, fast movements accurately. For most machines, you can punch in a line of code that will change the modes – from high speed mode to exact stop mode and everything in between. In high speed mode, it needs to be able to honor the programmed toolpath without significantly overshooting.
Otherwise, you'll have a lot of broken tools when your machine ends up overshooting and pushing your tool 0.080″ into the material instead of the intended 0.050″.
Aside from having fast, responsive servos to handle sharp changes in direction quickly, your machine needs to be a fast thinker.
For high speed machining, you might end up with programs with millions of lines of code. If your machine controller can't read the code fast enough, then all your potential efficiency from peel milling will be lost while your machine tries to figure out its next move.
Machines that are well equipped for high speed machining will advertise a high 'block look-ahead', often something to the tune of 10,000 blocks.
What this means is that the controller will read 10,000 blocks ahead of the current block to be able to 'plan out' the most efficient way of hitting this toolpath within the allowable tolerance. If your machine doesn't have this ability, then you might find that your feed rate never actually hits what you programmed it to be.
Cam System
This is fairly straightforward. In order to benefit from peel milling, you need to have software that is capable of it.
The good news is that peel milling has been around for a while, so the large majority of decent CAM packages will have something to offer.
They're not all created equal, though. Some allow you to have a tighter control than others. If you're looking at a CAM package for your shop, take your time and see how good both the CAM toolpaths and the postprocessed results are.
The reason that I say to pay attention to the postprocessor is that with peel milling, you will have a lot of small movements. You want this to be calculated accurately as arc commands (or splines if your machine has a Siemens controller) without rounding issues. If you have to resort to using G1 line motions because you keep getting errors on your machine controller saying that there's a problem with your G2 and G3 values, you won't be a happy camper.
Really, this is becoming less and less as a factor as peel milling becomes more mainstream, but even still, it's a factor to pay attention to.
When is Peel Milling Practical?
There's a reason that this isn't the only operation you can select in your CAM software: while it is a great solution, it can't be applied to everything.
Peel milling works best when you can really sink your tool deep in the material. In other words, if you're doing shallow pocketing, you'll be better off with another strategy.
How To Mill Slots In Steel Cut
Slotting
Trochoidal milling is very often the best solution for slotting, but again it really does depend on the feature geometry. For example, the slot might be so deep that the only reasonable way of cutting it is either with a slitting saw or an EDM. If the slot is 0.050″ wide x 1.000″ deep, no endmill will help you.
I find the sweet spot for trochoidal slotting to be where you can maximize the depth of an endmill that's between 50-75% of the slot width. In other words, a half inch endmill with a trochoidal toolpath will be an excellent choice for a slot that's 0.75″ wide and 1.000″ deep.
Pocketing
This is an excellent choice for deep pockets. The thin, light chips are easily blasted out of the pocket with and air blast or high pressure coolant, and the material removal rate is very high if you can use the full flute length.
Hard or Exotic Materials
When I'm roughing titanium, I use one of two methods: plunge milling or peel milling.
The material removal rates of plunge milling in titanium are second to none, but the leftover scallops can be a pain to clear out. They often require an excess of semi-finishing operations before you can run your finishing tool to complete the feature.
Peel milling, on the other hand, can often rough and finish in a single operation. Especially for deep and narrow features, it's hard to beat.
Peel milling really shines when it comes to hard and abrasive materials. Since it distributes wear along the entire flute length, it can be a great solution in applications where notch wear or chipping is common. Here are some materials where you should seriously consider using peel milling as a practical way of roughing:
- Titanium
- Inconel
- Cobalt-Chrome
- Hardened tool steels (above 50 Rc)
- In general, any material that is work-hardening, abrasive, or hardened.
When Peel Milling Doesn't Make Sense
When you can't use a good amount of your flute length, then peel milling probably isn't a great option.
For example, if you have a shallow slot – let's say 0.750″ wide x 0.375″ deep – you'll be better off going the traditional route of using a 3/4″ endmill and burying it.
How To Mill Slots In Steel Hole
If it's an exotic or hardened material, peel milling might make sense even if you can't use much flute length. Sometimes the solution is to simply use a smaller cutter. Or look into other strategies like hi-feed cutting (low Z depth, full cutter width stepover, and very high feed).
Ultimately, you'll get a good feel for it once you've tried it a bit. Maybe try programming the toolpaths a few different ways and see which one seems to be able to achieve the best cycle times. Just make sure that your machining conditions are set appropriately for each strategy – don't use standard feed rates for peel milling.
There you have it, you're ready to take on the peel milling world.
Do you have any tips and tricks for high speed machining? Or do you have any questions about peel milling? Share them in the comments below!